
How an organ pipe is made
Metal pipes are generally made from an alloy of tin and lead, the composition determined by the organ builder for tonal or visual reasons.
A higher ratio of tin provides more shine, greater durability and an increased potential for harmonic development. Zinc may be used to make large bass pipes and copper is sometimes used for display pipes.
In the casting room, tin ingots and 'pigs' of lead are melted in a pot before being transferred to a rectangular container at the end of a stone casting bench.
As the container is pushed along the bench, a thin layer of molten metal flows from a slot. When cool, the sheet of metal is planed to the required thickness by machine or hand.
The next stage is to form the pipes. Pieces for the body and foot are scribed, cut to a pattern, rolled then beaten around cylindrical or tapered mandrels to create their shape.
The surface of the metal is protected with a size made in our workshop from gum arabic. This prevents molten solder from spreading beyond the seam and also insulates the pipe body from heat.

The pipe maker is now looking down on two edges which require soldering. First the sizing is scraped from each edge and a 45 degree bevel created to allow the solder to flow along the seam. This is a skilled process as the melting point of the solder and of the pipe metal are nearly the same. The pipe body is then gently rounded with a beater.
​
The next step is to form the labia, behind which lies a horizontal metal plate, the languid. First the upper and lower lips are shaped, then the languid is soldered to the pipe foot which is, in turn, soldered to the body. Finally, the mouth – an aperture above the languid – is cut. Its dimensions are crucial to the tonal quality of the finished pipe. The pipes are then cleaned and polished ready for the voicer.
A demonstration in our workshop of hand-planing metal, in this instance 25 per cent tin, using an old plane, cabinet scrapers and a polishing scraper.
This video was made during a visit to our workshop by the American organ builder, Jim Steinborn. It was shot and edited by William L Rogers and we are grateful to them both.
Some tools of our trade

Flatting tools
​
These are for pressing the upper and lower lips to a pre-determined proportion. We have a full complement of all mouth widths.
Chris Shires demonstrates our method of rounding pipe feet using a block and wooden mandrils in this video. The tools he is using are more than 100 years old.
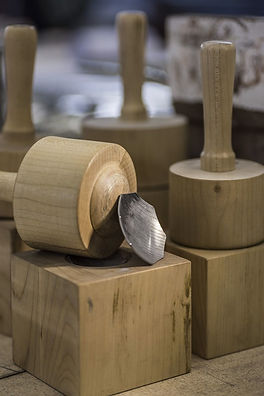
Doming tools
Used for the lids on canister tops, the dome ensures that the metal will not vibrate when played.

Hand plane
The base is made from lignum vitae which helps prevent any wear over the years. The angle of the iron blade is very different to a traditional wood plane
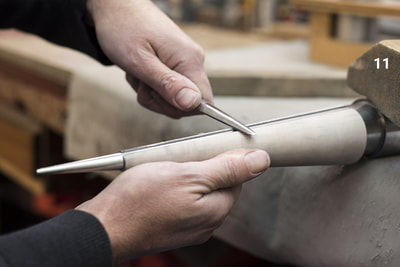


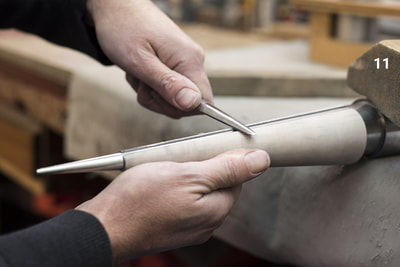
In this series of slides, the various early stages involved in making a flue organ pipe are demonstrated.