top of page
Search


Restoration expert George works his magic on a Willis organ pipe
Many of our customers believe that our renowned colleague and restoration expert, George Fowler, is as much a magician as a pipe maker....
Chris Shires
6 days ago1 min read
Â
Â
Â


Bedford School Chapel's new Drake organ built with pipes by Shires
We are pleased to have supplied the metal flue and reed pipes for the exciting organ being built by our friends William Drake in the...
Robert Cockroft
6 days ago1 min read
Â
Â
Â


Fine mixtures made for organ builders across the world
Terry Doyle, above, uses a mandrill to shape pipes – 330 of them – for a V-VI rank mixture of 80 per cent tin destined for an organ...
Chris Shires
Jun 171 min read
Â
Â
Â


Replica 17th century flue pipes for Gloucester Cathedral
Chris Shires rolling metal for the replica pipes destined for Gloucester Cathedral James Atherton, head voicer at Nicholson's, shows one...
Chris
Jun 161 min read
Â
Â
Â

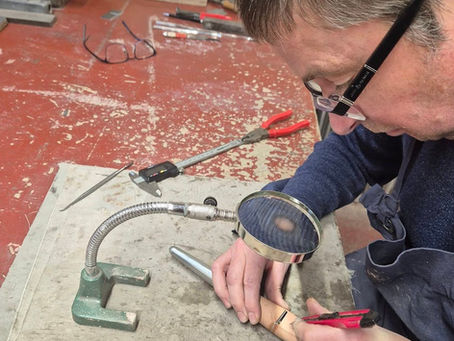
Gift pipes to celebrate achievement or milestones
Here is Terry Doyle making decorative gift pipes for our stock. He is following a standard pattern, but others can be made to order. This...
Chris Shires
Nov 20, 20241 min read
Â
Â
Â


A Tuba with Skinner scales made for America
Here's a Tuba 8 ft destined for an instrument in America. It features Skinner scales and shallots in the same style. We are specialists...
Chris Shires
Nov 14, 20241 min read
Â
Â
Â


Repairing 19th century Conacher pipes with the original pipe maker's tools
Here are some before and after pictures of repairs carried out on a 16ft Waldhorn from the Victoria Hall, Hanley. Originally named a...
Chris Shires
Oct 31, 20241 min read
Â
Â
Â


Metal reeds and flues for new William Drake organ
We are delighted to be involved in a new project for our friends at William Drake, organ builders. They have been commissioned to build a...
Chris Shires
Oct 14, 20241 min read
Â
Â
Â


Getting around to burnishing an organ pipe...
In the video below, Chris Shires demonstrates how burnishers are used at Shires Organ Pipes to make pipes perfectly round. Soap and...
Chris Shires
Sep 16, 20241 min read
Â
Â
Â


George returns to a Tierce he made 40 years ago
A customer asked us to make three new pipes for an existing Tierce to adjust the scale of the rank. Upon investigation we found that our...
Chris Shires
Aug 20, 20241 min read
Â
Â
Â


Facade pipes in full glory on a new Mander organ
We are delighted to see our facade pipes in their full glory on a new two-manual, mechanical action organ. It has been built by Mander...
Chris Shires
May 8, 20241 min read
Â
Â
Â


Replacement pipes made for organ in America
It's satisfying to see our work in place and a pleasure to have worked together with our colleagues at Wallace Pipe Organs in Maine, USA....
Chris Shires
May 8, 20241 min read
Â
Â
Â


Decorative open diapason pipes for Mander organ
We have now completed the decorative Open Diapason facade pipes for Mander Organ Builders who are building a new two-manual instrument in...
Chris
Feb 21, 20241 min read
Â
Â
Â


George offers crash course in organ pipe repair
Organ builder Nick Adams asked us to repair these bent Conacher Salicional pipes from St John's Church, Canton, in Cardiff. They acquired...
Chris Shires
Jan 17, 20241 min read
Â
Â
Â


Four foot Octave rank made for a 1931 Reuter organ
Ryan Luckey, vice president of the Nebraska-based Bedient Pipe Organ Company, asked us to make a four foot Octave of 73 notes to...
Chris Shires
Jan 17, 20241 min read
Â
Â
Â


George repairs Victorian dented Beaulieu pipes
We were asked by Joost de Boer of William Drake Organ Builders to repair some pipes from a Robert Mirrlees organ, dated 1842, in Palace...
Chris Shires
Oct 25, 20231 min read
Â
Â
Â


A rare order for a Flûte à Biberon – a 'baby's bottle' flute
It's very rarely that we are asked to make a Flûte à Biberon, but here are the completed 4' pipes for a British organ builder. The stop...
Chris Shires
Oct 17, 20231 min read
Â
Â
Â


Putting the buzz back into some damaged Walker reeds
Buzard Pipe Organ Builders has announced an exciting organ project for St. James Episcopal Cathedral in Chicago. It will see the...
Chris Shires
Sep 3, 20231 min read
Â
Â
Â


Three upperwork stops for organ in Illinois Catholic church
We have been asked us to make three stops for the refurbishment of the organ at St Giles Roman Catholic Church, Oak Park, Illinois, USA....
Chris Shires
Aug 16, 20231 min read
Â
Â
Â


The art and craft of making decorative gift pipes
After Terry Doyle had finished working on some very large pipes, we thought it was only right to give him a sit-down job. So he designed...
Chris Shires
Jul 26, 20231 min read
Â
Â
Â
bottom of page